Designed and Made By ___________
Senior Capstone + Self-Initiated Internship
Lamps designed and made by myself, Mike Demis, Ed Nelson, Harvey Nunez, Tim McSorley, and Mike Hull—manufacturing line operators at Forms + Surfaces. I designed the lamps to be designed by these operators as they moved through the production floor, highlighting their individuality, creativity, and expertise.
The project proposes a new paradigm for the design-manufacture workflow, exhorting a healthier relationship with our objects through a greater consideration of not just where they come from or how they’re made, but who makes them.
The other half of the project is a 152 page book I wrote, photographed, and designed. It tells the story of the lamps, and the stories of the people who made them.
Industrial Design
Design Research
SolidWorks
Keyshot
Design for Manufacture
Design for Assembly
Soldering, Simple Circuitry

Sophomore year, my cohort and I visited a number of local manufacturing sites for our manufacturing class “How Things Are Made.” Seeing these processes and their operators firsthand, was eye-opening.
Continued training in our ID program deeply instilled in me values of sustainability, hands-on making, and the charge to use our craft to materialize more personal, inspired agendas.
Going into my senior capstone, I knew I wanted to make work that challenged peoples’ relationship with the material world— through a greater awareness of not just where our objects come from, but who makes them.
Continued training in our ID program deeply instilled in me values of sustainability, hands-on making, and the charge to use our craft to materialize more personal, inspired agendas.
Going into my senior capstone, I knew I wanted to make work that challenged peoples’ relationship with the material world— through a greater awareness of not just where our objects come from, but who makes them.
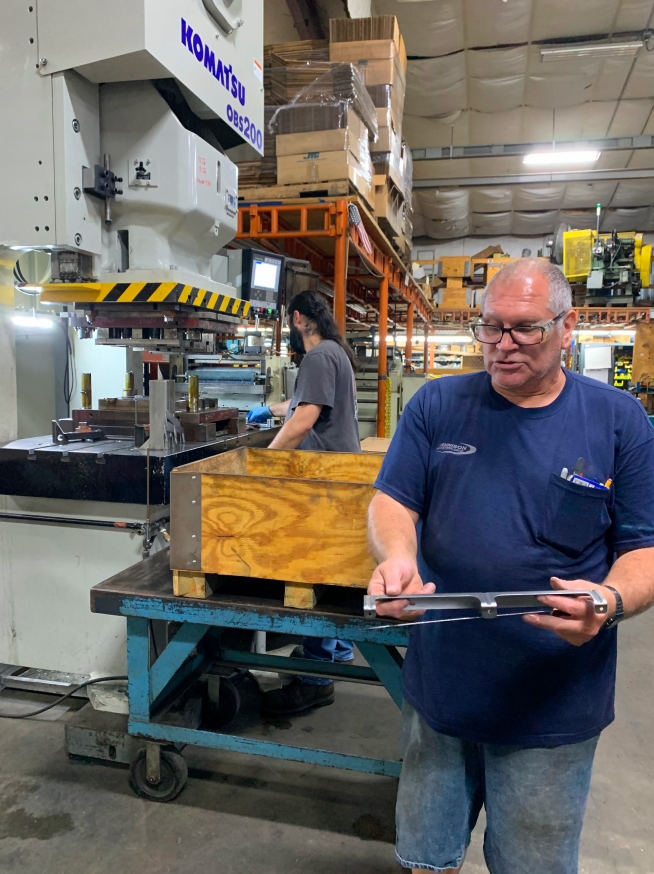
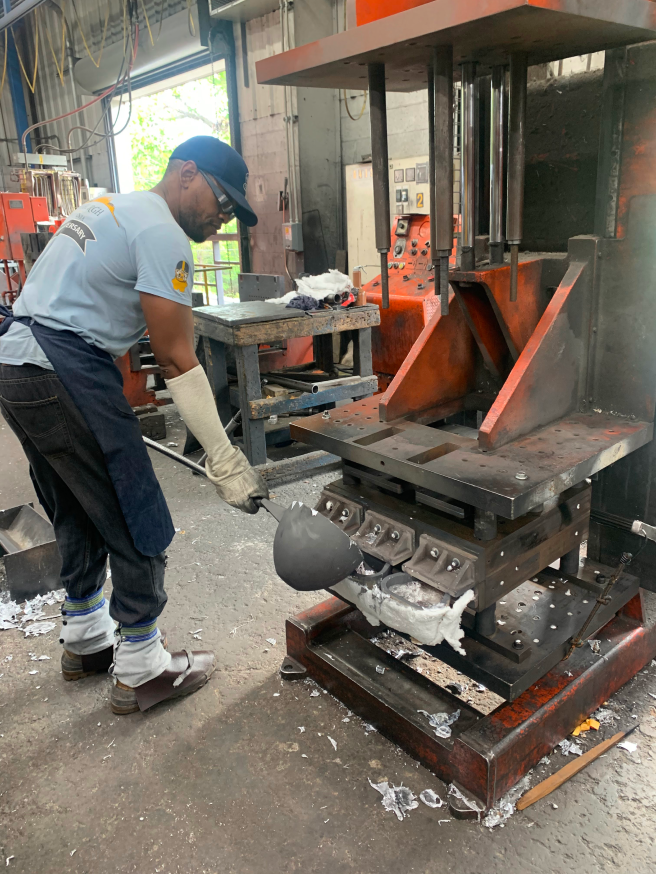
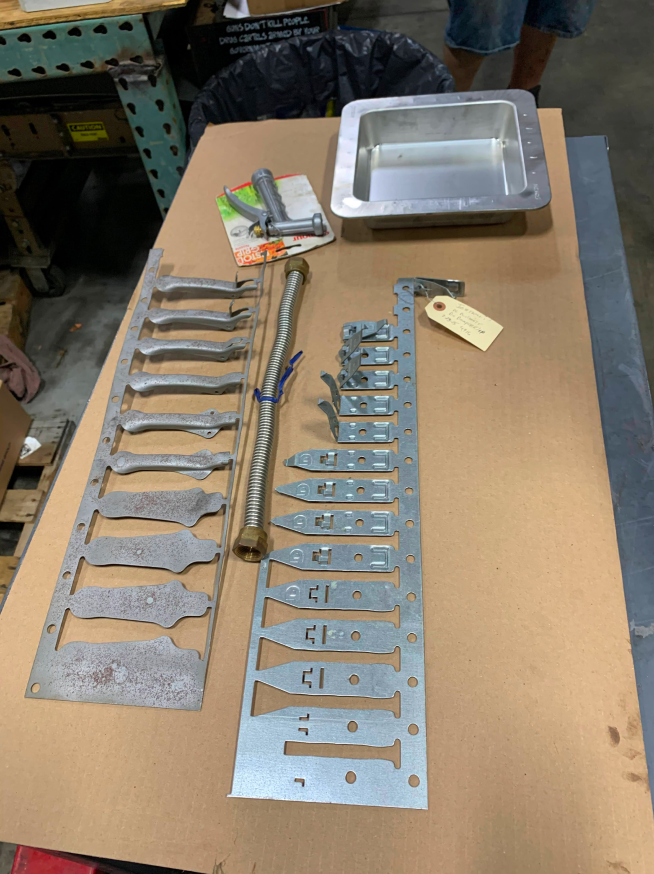
Snapshots from the manufacturing sites.
Problem Space
The majority of people, when acquiring, interacting with, and disposing of objects, have little idea how they come to be.Though sometimes we may consider who designed our objects, rarely do we give thought to whose hands actually bring them into the world.
I believe that this fragmented relationship between consumers, designers, and manufacturers contributes to our throwaway culture.
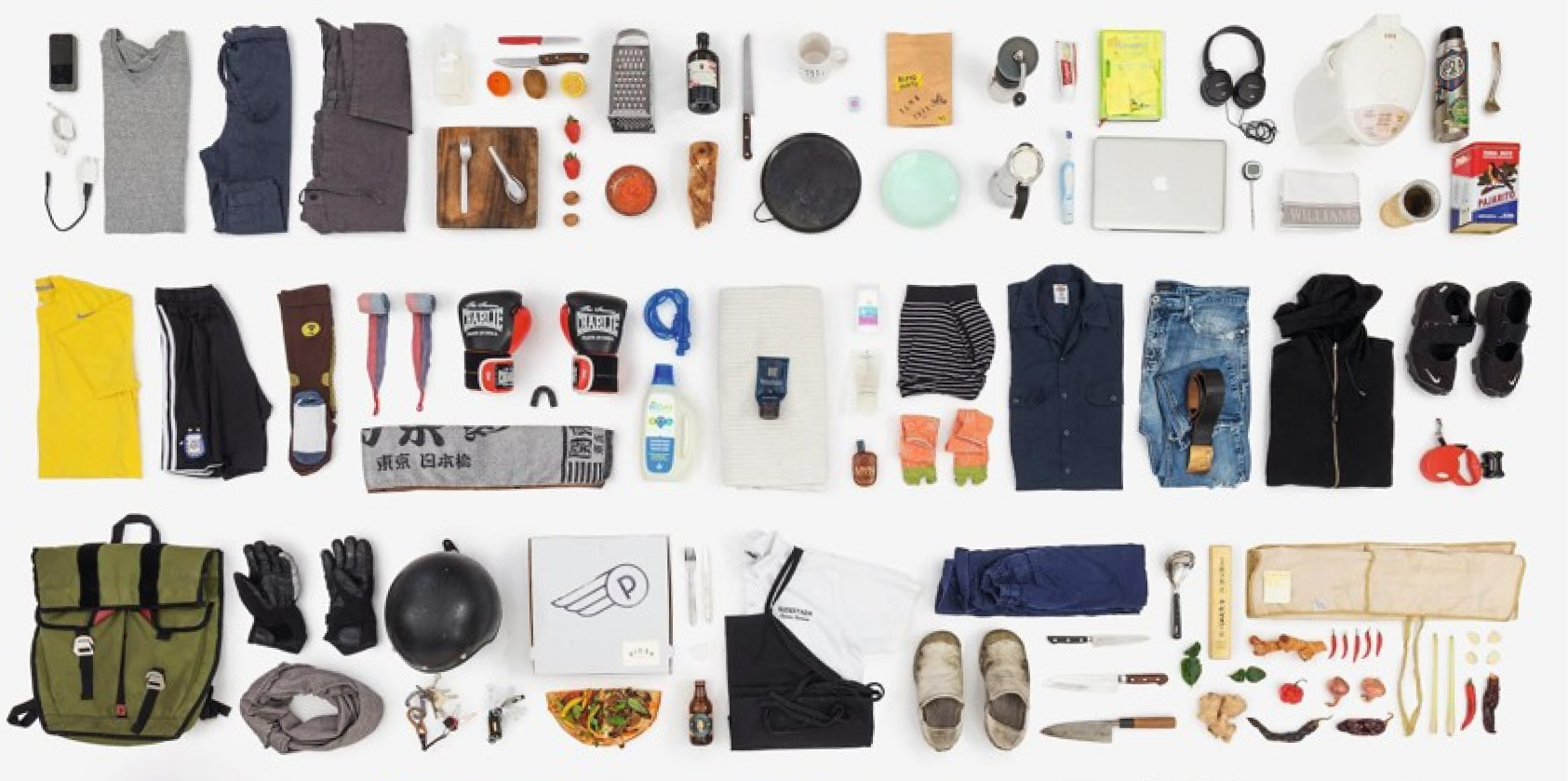
Forms + Surfaces
In response, I reached out to and self-initiated an internship and design and development project with Forms + Surfaces, a local architectural products manufacturing company.
My goal was to create a product that would give operators more agency during the production process, highlighting their individuality and creativity, and reminding interactors of the people who put together our object world.

The Lamps
In the end, I worked with five of their operators to produce six lamps. Each of the lamps are unique in that the operators at each step of its manufacturing process were invited to variably affect the product’s form and finish, following an “add to the drawing and pass the paper down” model:
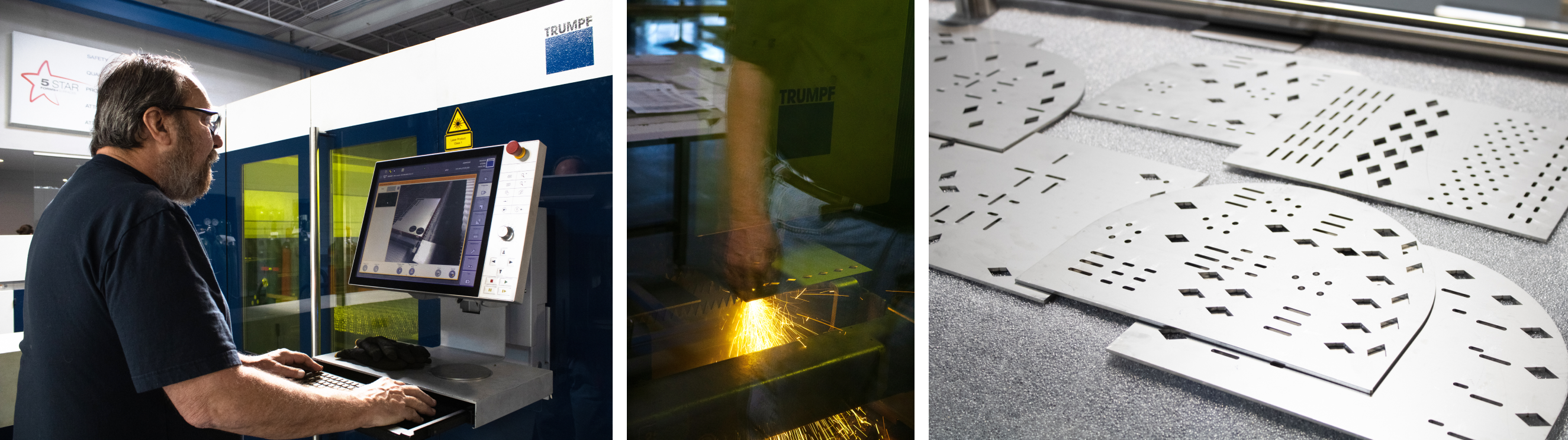
The laser programmer arranged four provided decorative shapes on the main lampshade pieces to cut a unique pattern onto each one.
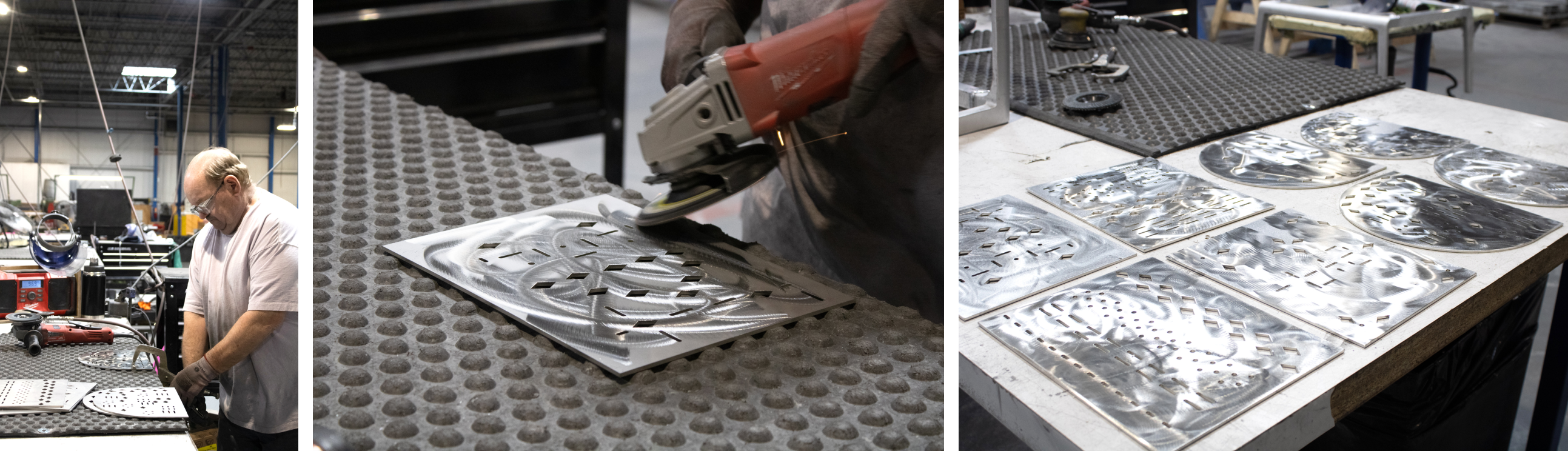
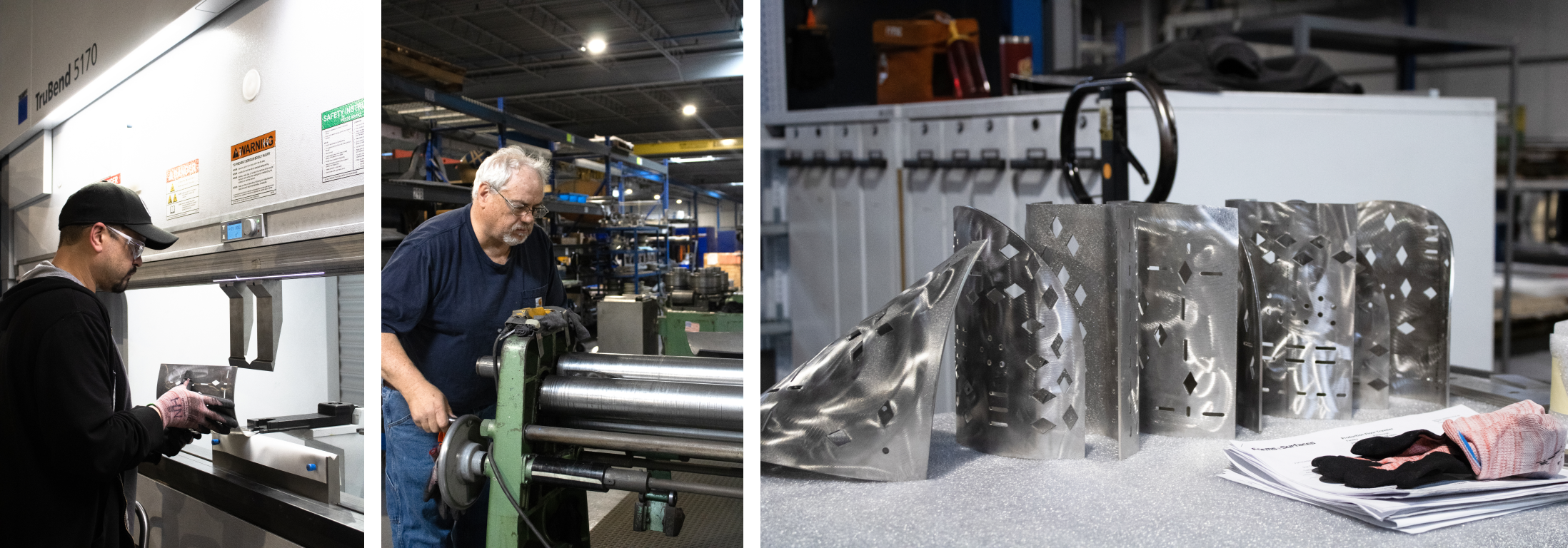
The press brake and roll forming operators bent and rolled those lampshade pieces using their respective processes.
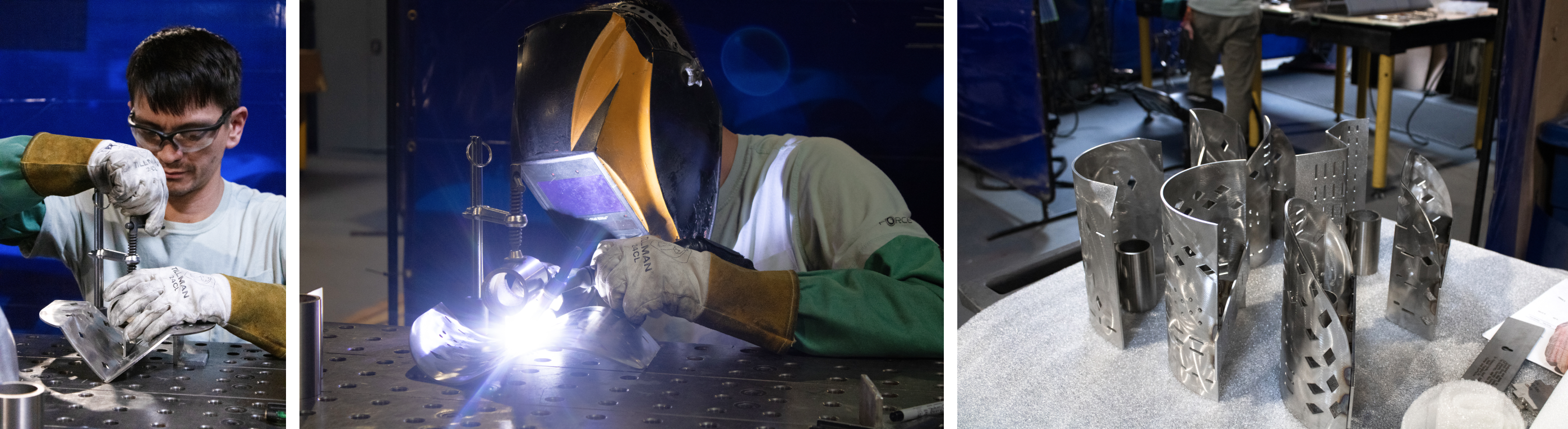
Finally, the welder welded those lampshade pieces to the provided standard parts to turn them into the final lamp forms.
The result is six lamps that follow the same form language, but which are all different as a compounded result of the varied ways each operation was employed.
They speak to the unique expertise and skill sets of each operator, highlighting their personal touch and creativity.
They speak to the unique expertise and skill sets of each operator, highlighting their personal touch and creativity.
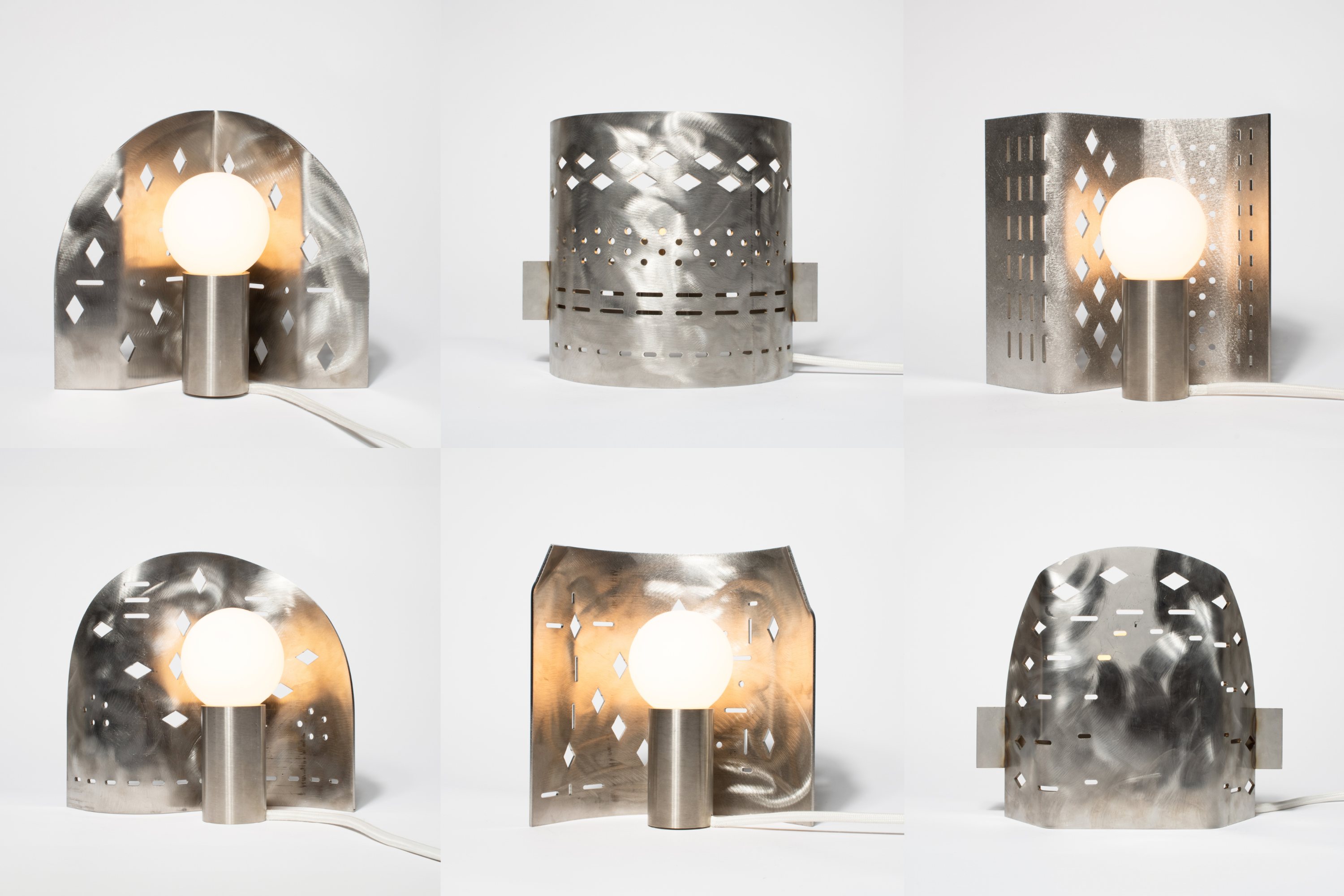

Process—First On-Site
A first tour of the manufacturing site to kickstart the project provided understanding of the capabilities I might employ.
Among those that stood out were laser-cutting, brake forming, roll forming, welding, and various finish options including powdercoating and sandblasting.
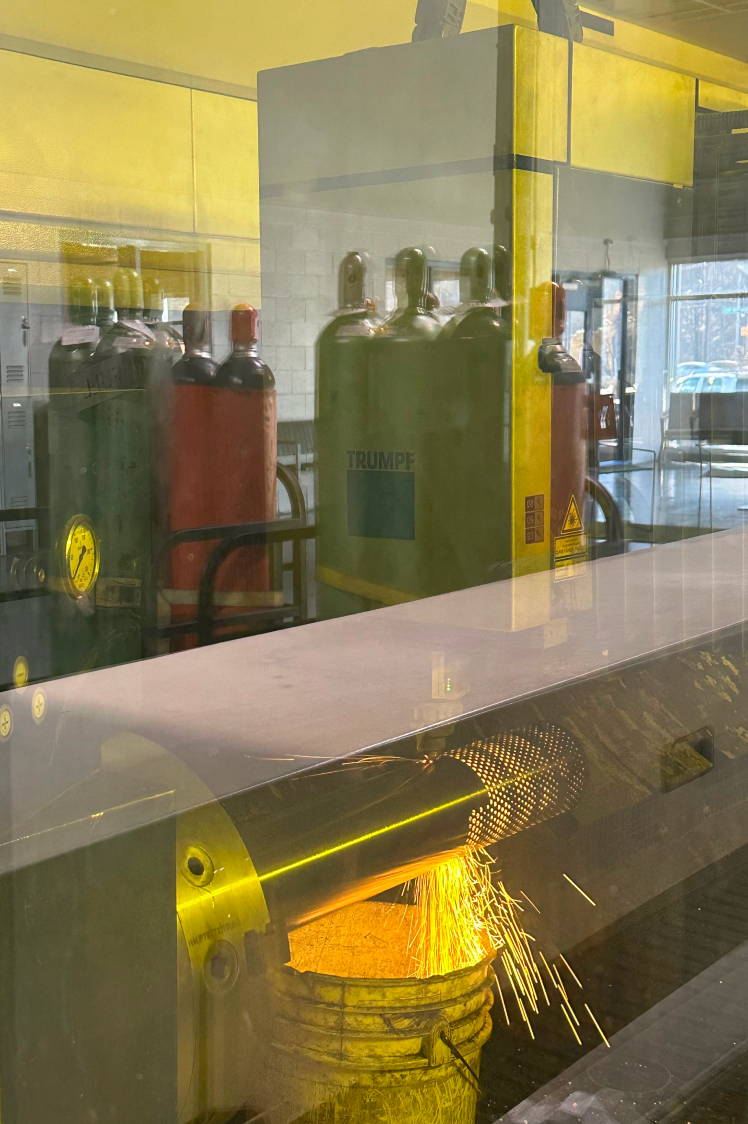
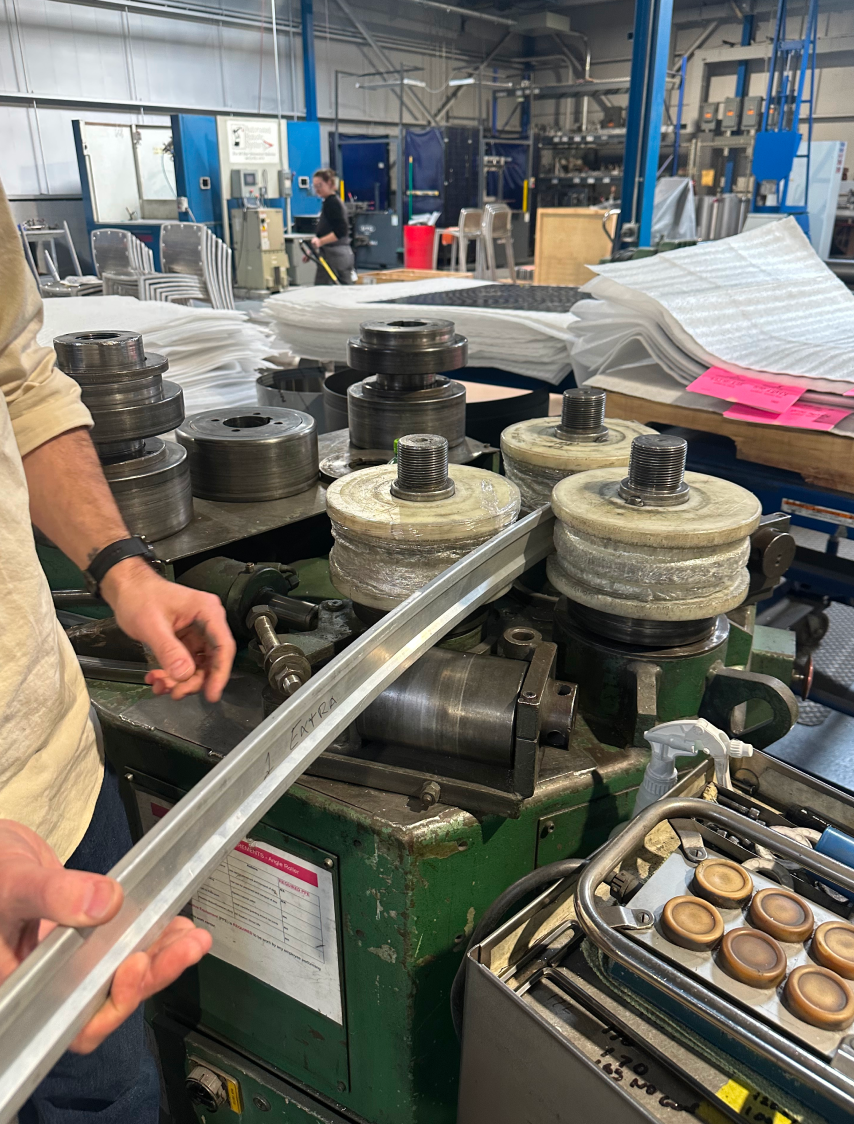
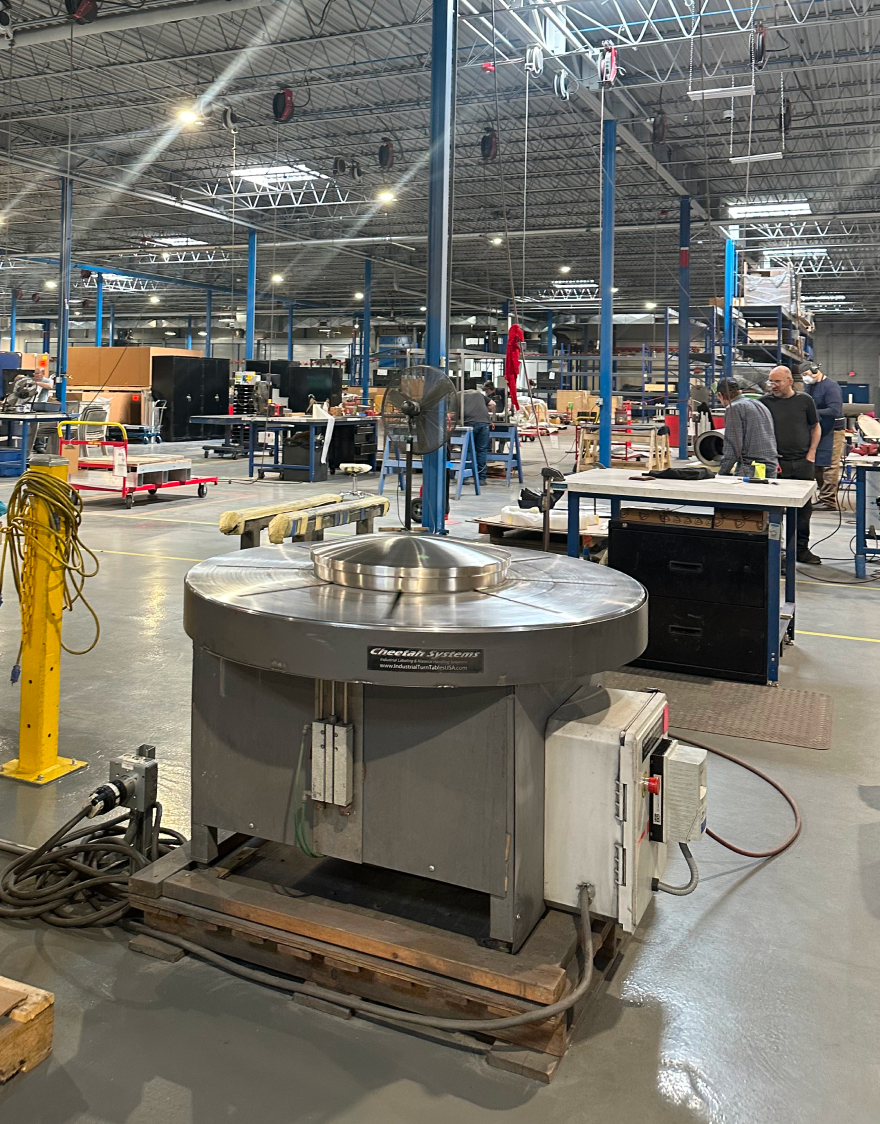
Initial Brainstorm

End tables with variable top and bottom surfaces, to be assembled with legs bent at variable heights with variable radii.
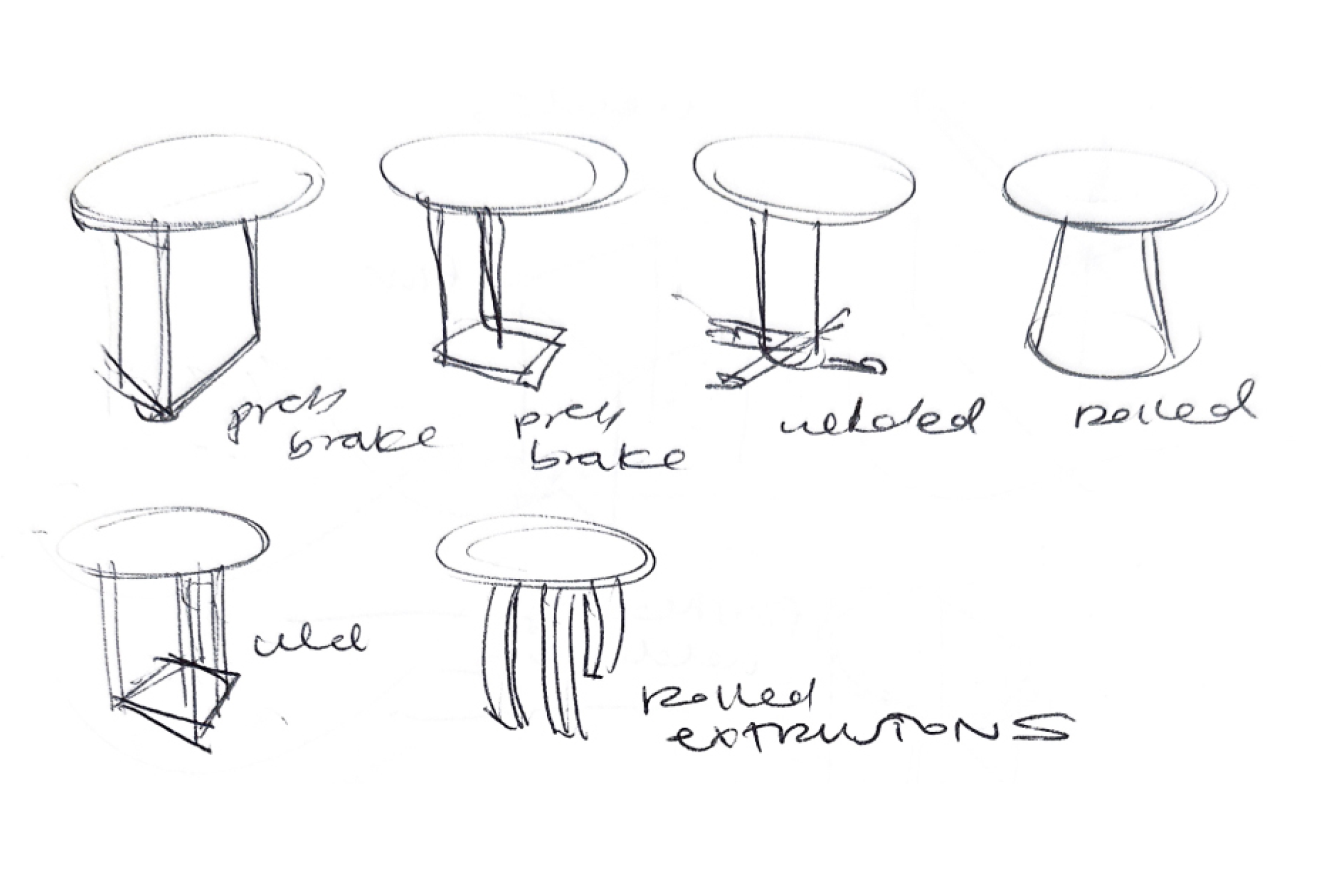
Tables with a standard top, highlighting variably formed and constructed legs.
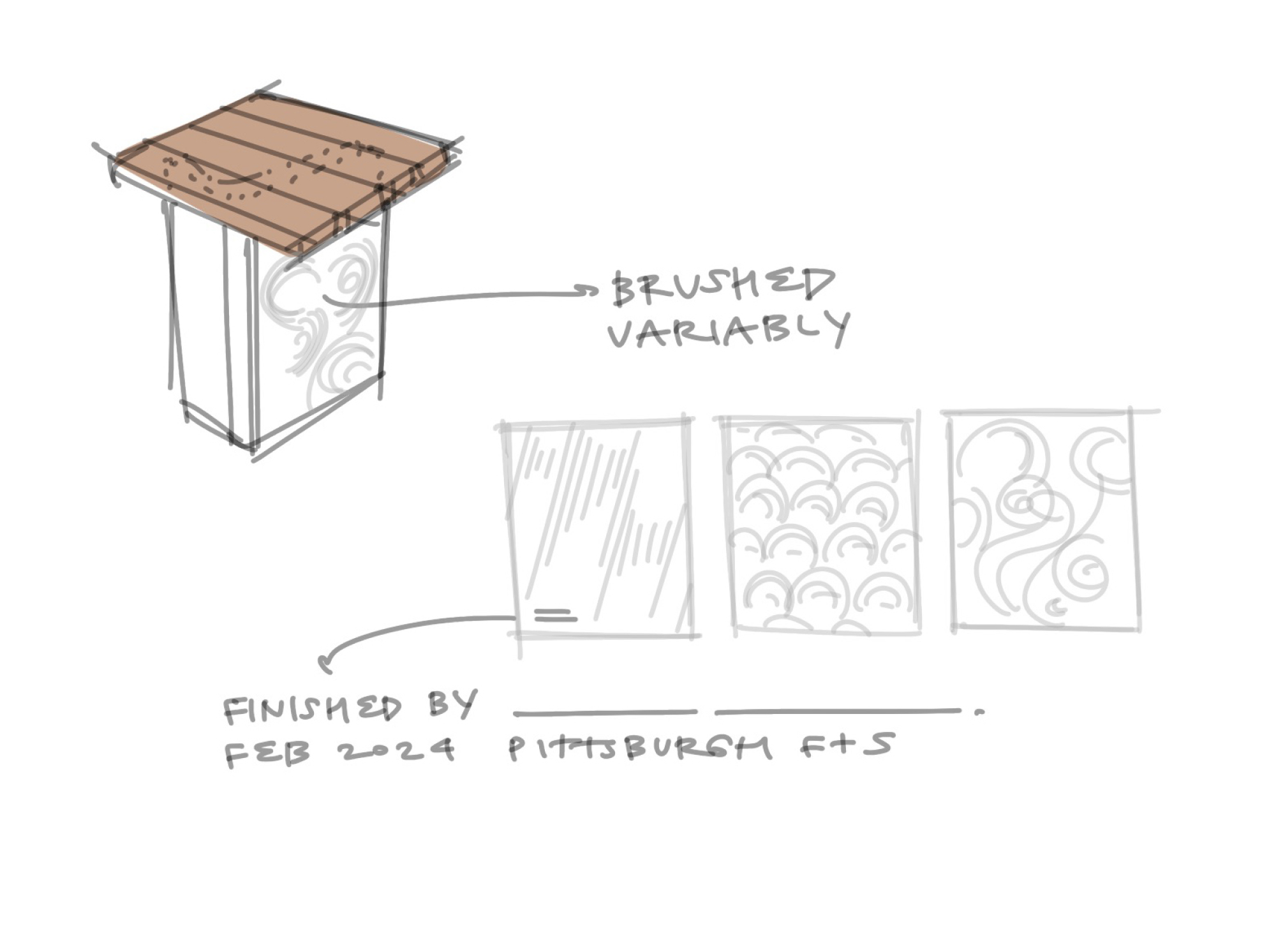
Tables with a standard top, accentuating the variably brushed metal legs.
︎︎︎ However, many of these initial ideas afforded either too much variability (like an exquisite corpse game, where participants have no idea how their contributions will be combined to create the final image), or not enough.

Examples of Exquisite Corpse drawings
Workflow Development
I realized that a workflow which affords a greater sense of agency would be one where the operators consciously affect the final form of each piece, in sequence, following an “add to the drawing and pass the paper down” sort of model. In doing so, each person employs their unique expertise and experience to creatively respond to the design decisions of the person prior.
I set up and user tested a mock assembly line to simulate this process:
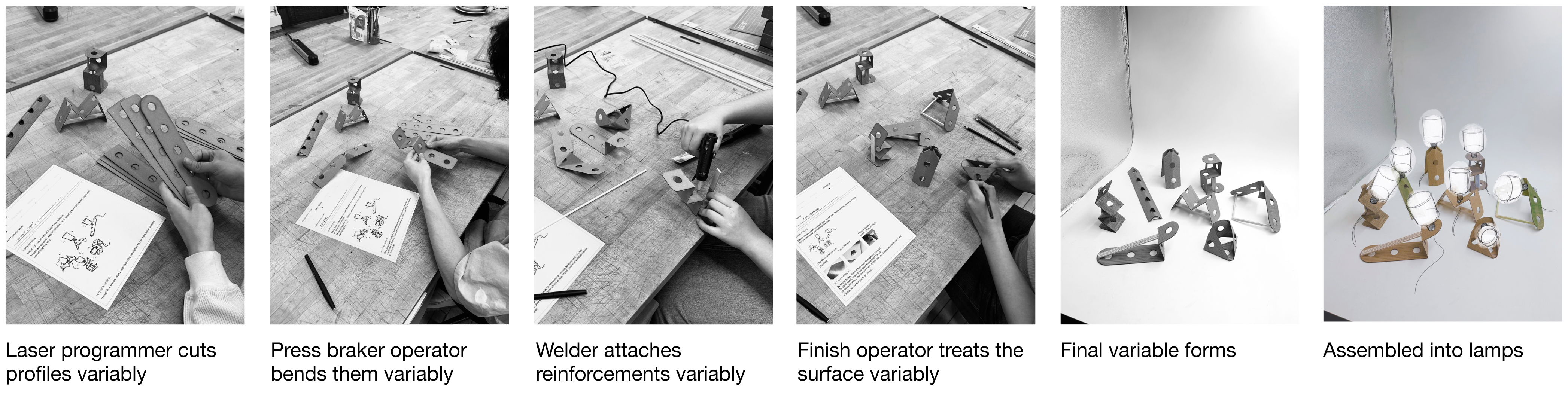
Insights
Speaking to the operators about the proposed workflow provided insight on not just the nuances of their respective operations, but also their personal and creative interests, which all informed the lamp’s design:
For example, when speaking with the laser programmers, I learned that they could duplicate and arrange individual shapes from a DXF on the programming software itself. As a result, I designed four decorative shapes to be freely arranged on the pieces to be laser-cut.
Harvey and Tim, the press brake and roll forming operators, explained that they often work collaboratively to achieve certain designs, which informed an open-ended forming step which left room for that back-and-forth.
Mike, the welder, expressed a personal interest in product design and “being on the other side of the manufacturing process,” so I tried to afford greater agency at the welding step, requiring aspects of problem-solving and functionality in addition to aesthetic sensibility.
Form Refinement
It was a unique challenge to design not an object, but the process for these objects to be designed.
Additional considerations included the available material stock (sheet thicknesses, tube sizes), and assembly considerations using off-the-shelf lighting parts.
My goal was to afford a worthwhile and equal amount of agency at each operation, while maintaining a cohesive, distinct, and beautiful form language.
On the Floor
Many thanks to the design team at Forms + Surfaces for helping me create the shop drawings to communicate the process with the manufacturing floor.
Wiring and Assembly
Once the lamps were made, I brought them back to campus and assembled and wired each one by hand.
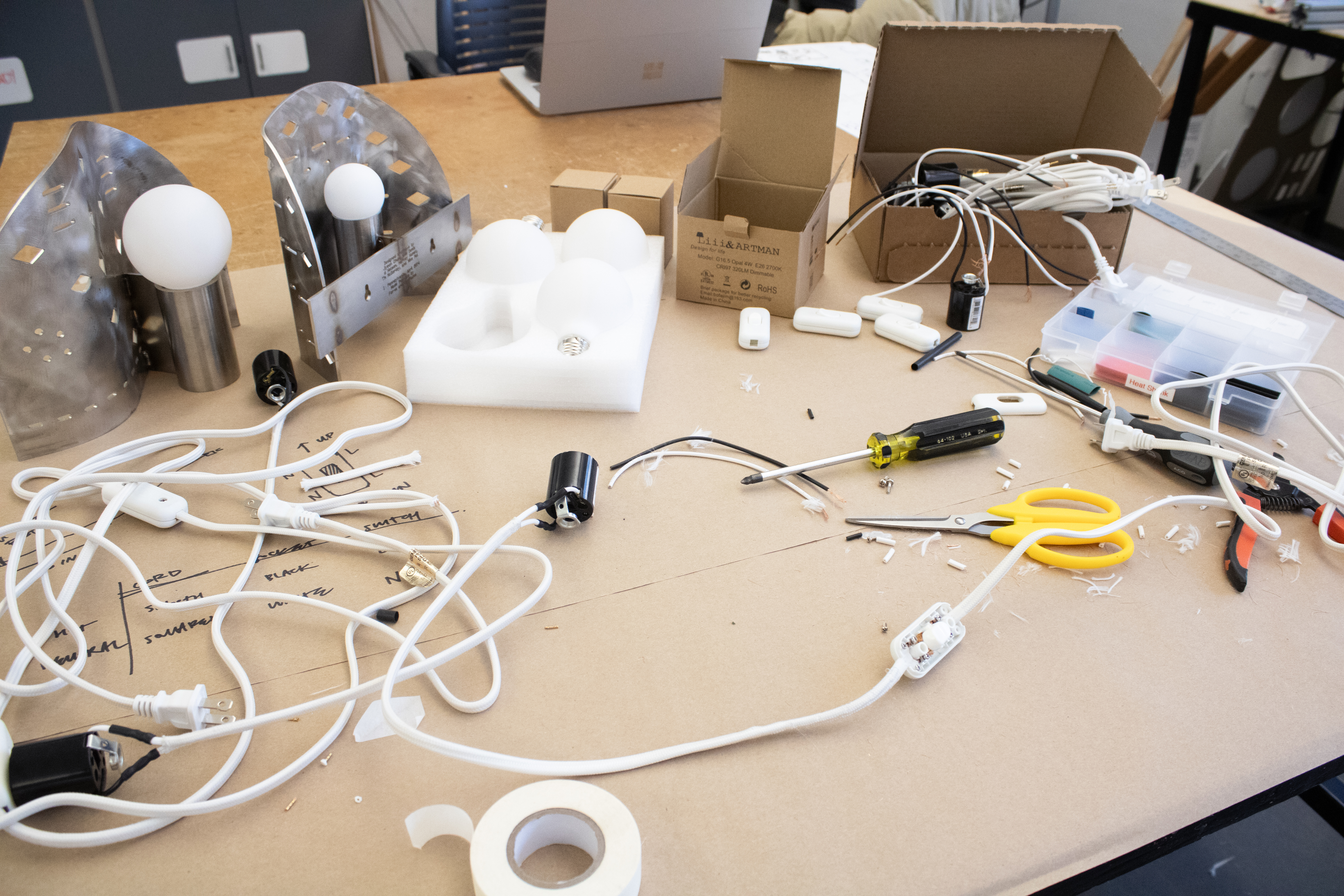
Documentation
Photographing with Dylan Vitone. We scoured several buildings across campus and their corners to find the perfect backgrounds.
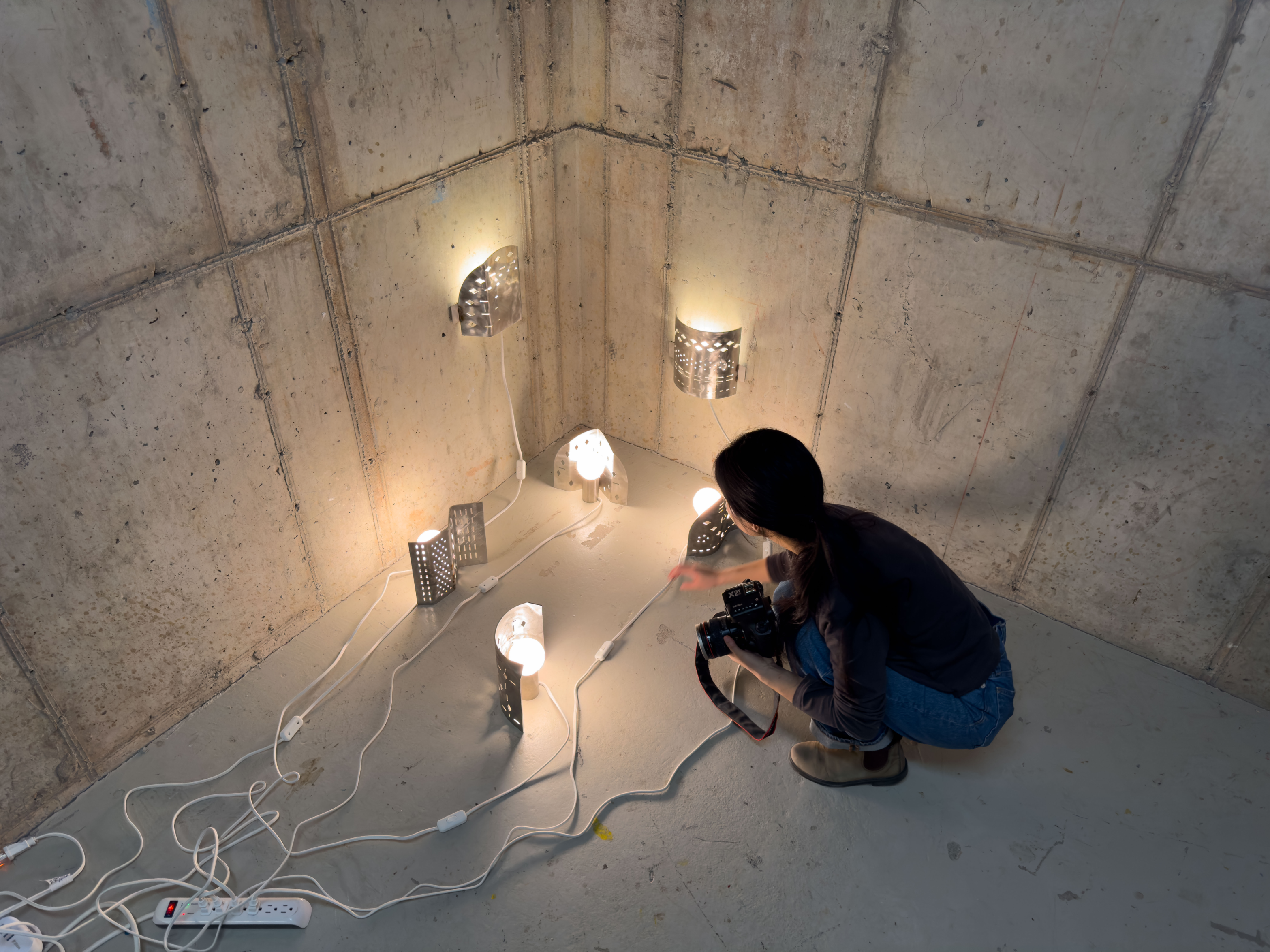

Designing The Book
While working with the manufacturing line operators, I was also interviewing and photographing them. To me, this project was ultimately about the people behind our object world, so an equally important aspect was to create this book containing their portraits and stories.
The book is organized around five chapters, each named for the person at the respective production step. It opens with the shop drawings and/or instructions they were provided. From there, photographs of them and their working on the lamps are paired with text from an interview about their work and life.
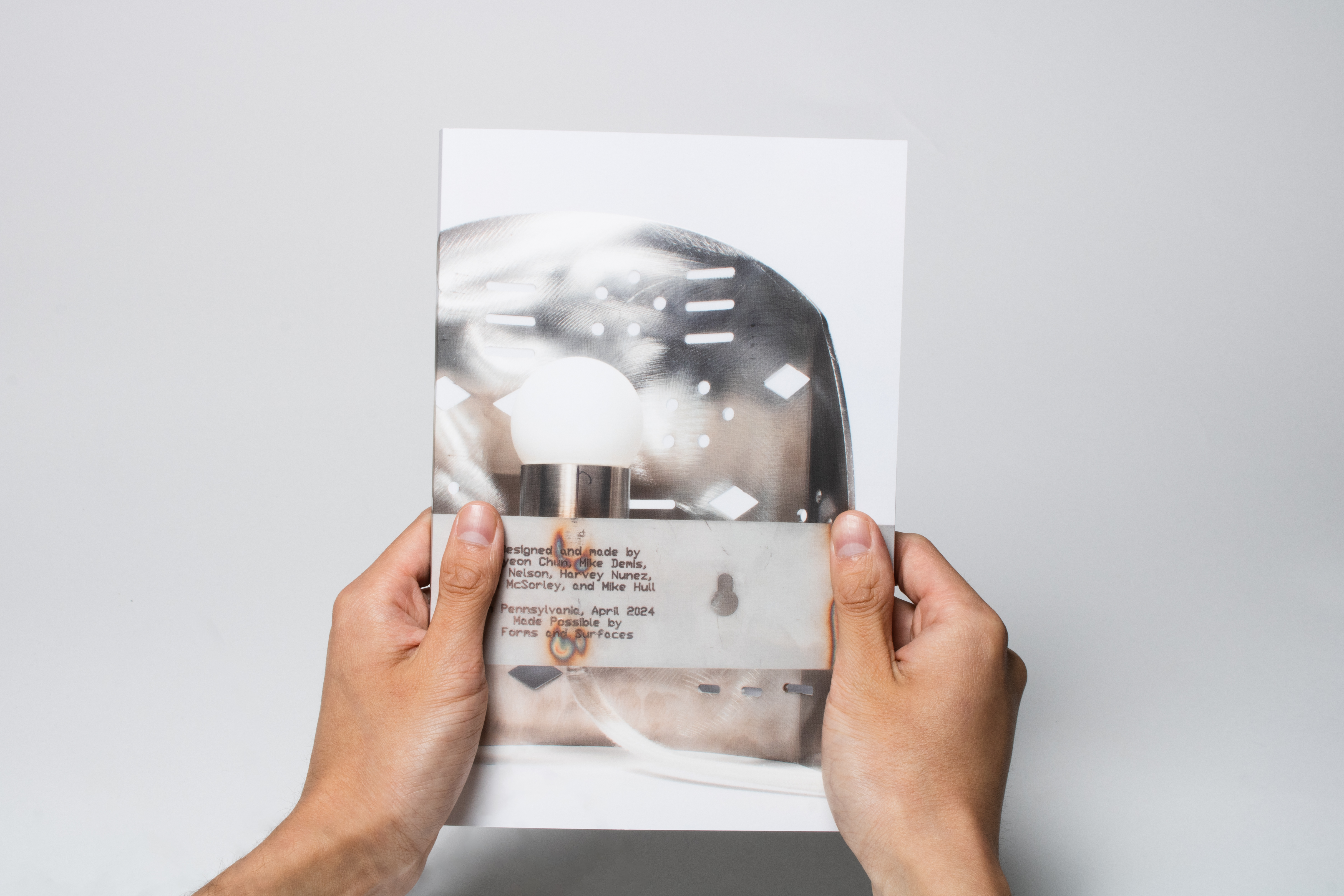
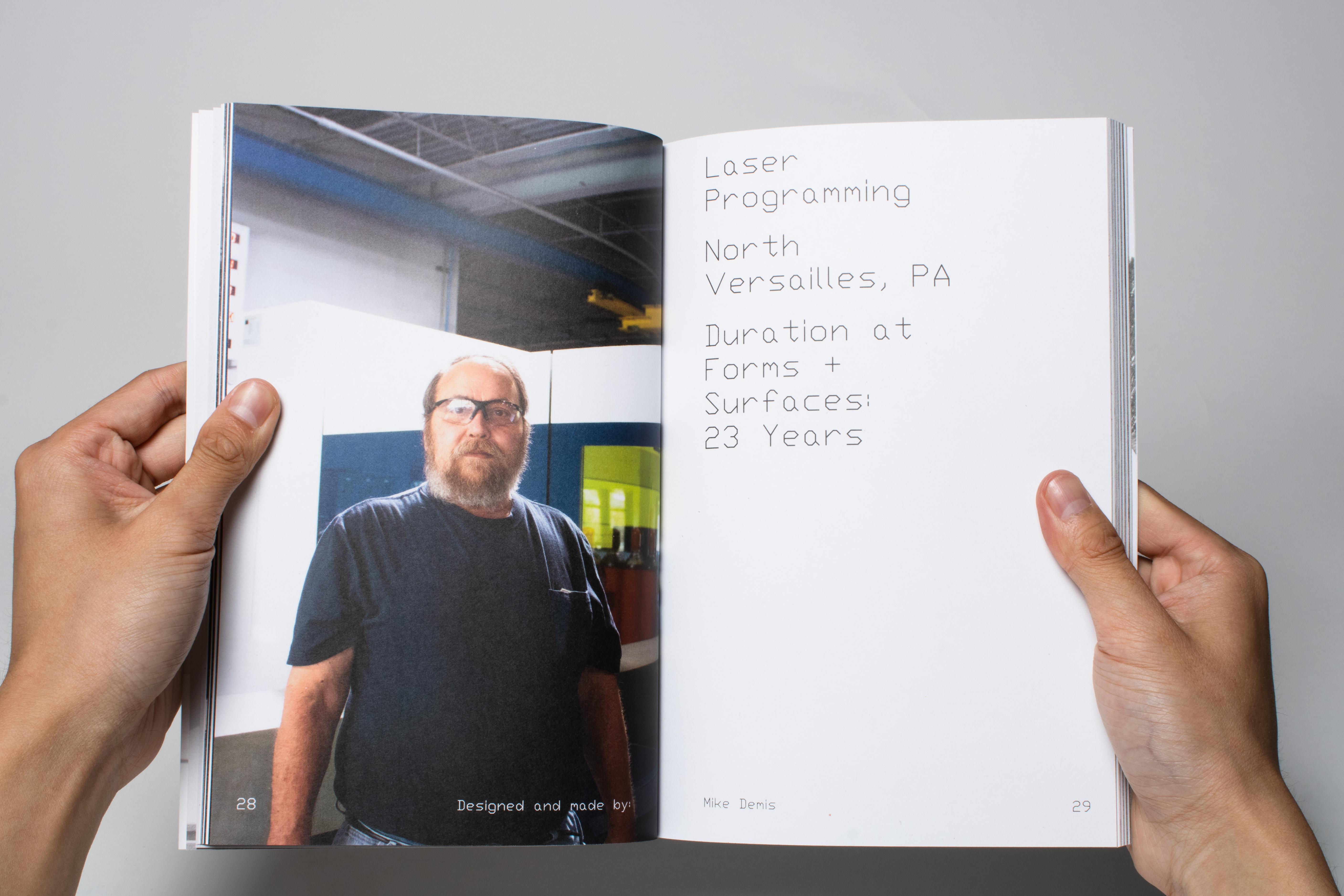
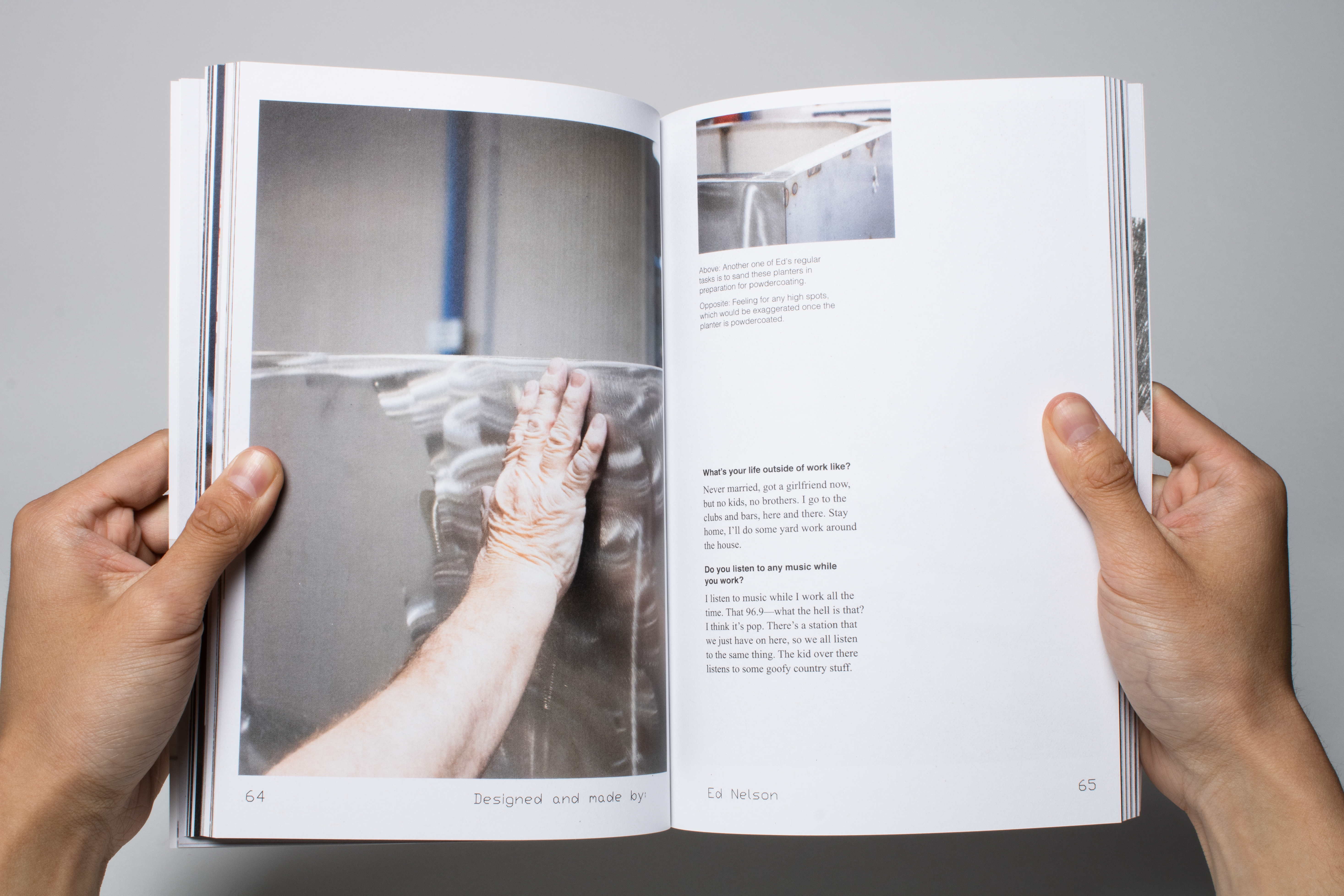

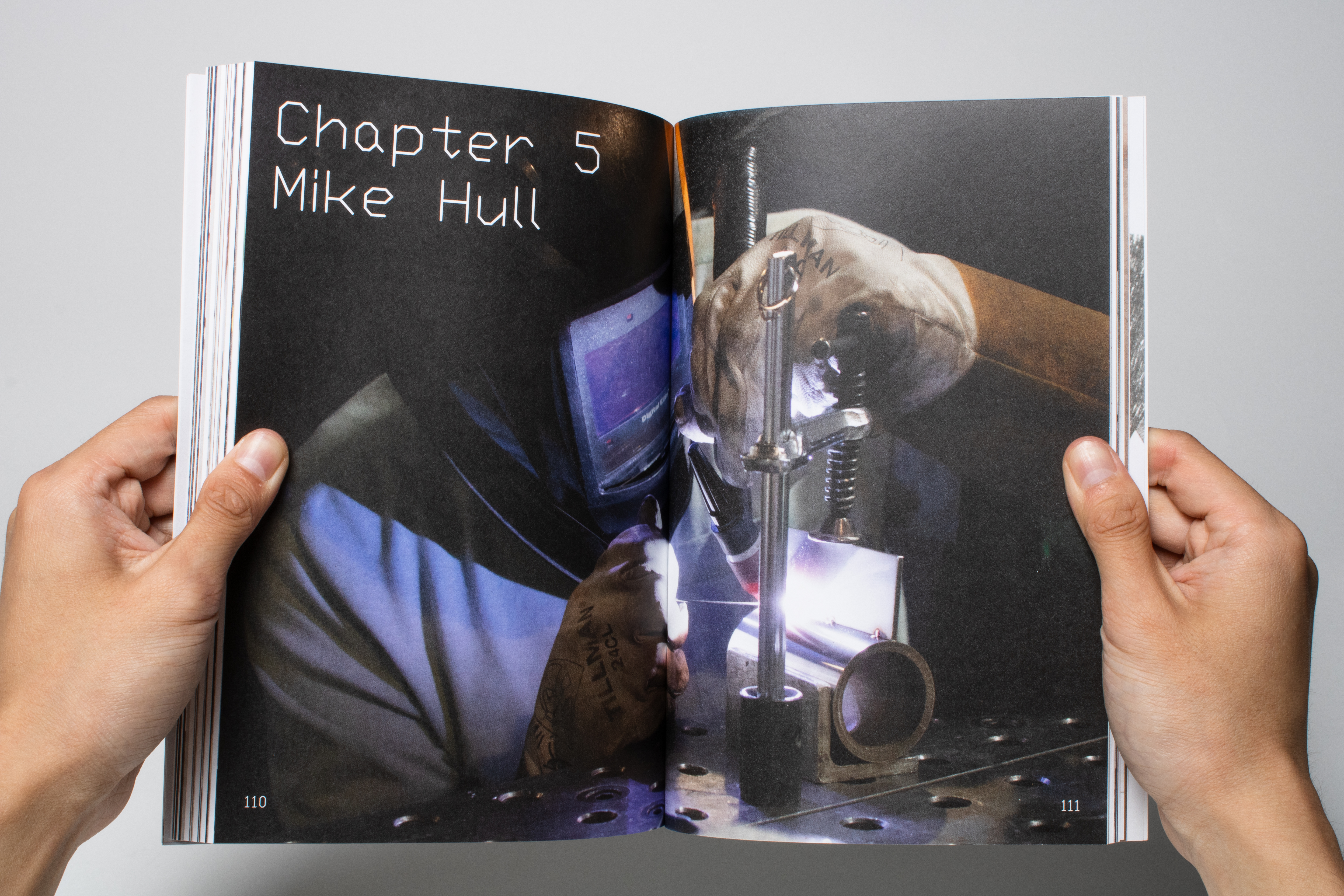
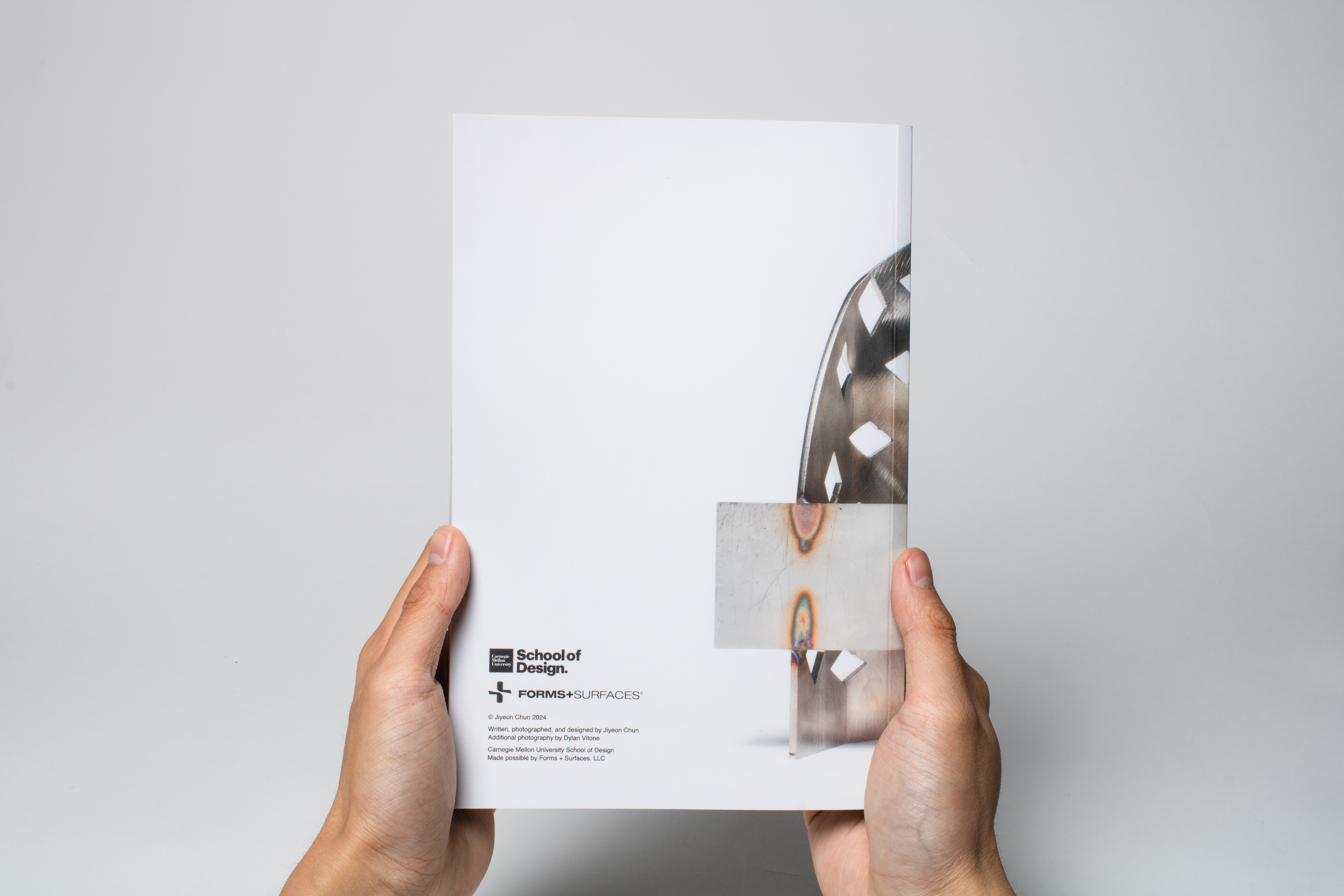
I had the immense joy and privilege to give them each a copy at the end of the project.
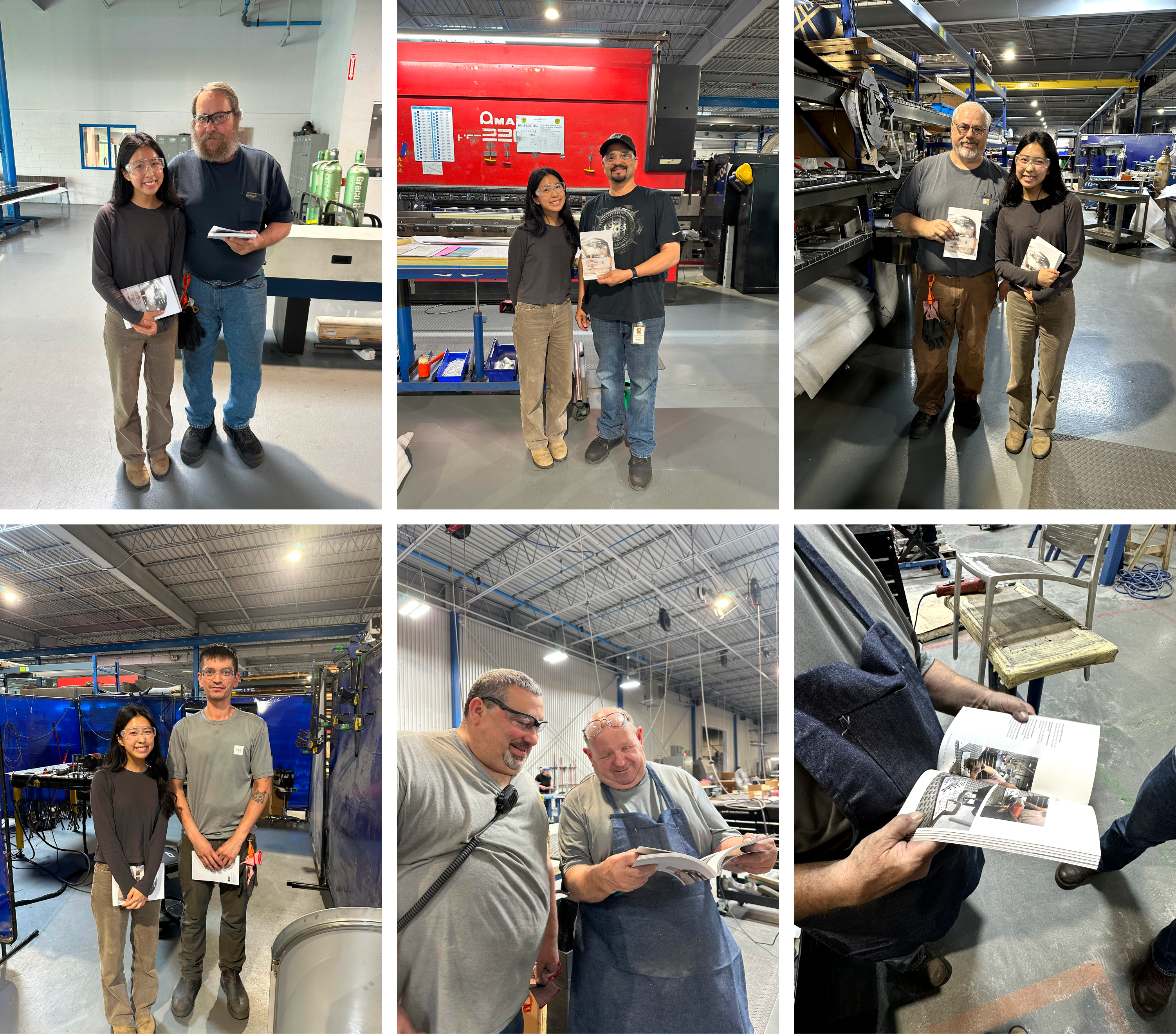
Thank You
Mike Demis, Ed Nelson, Harvey Nunez, Tim McSorley, and Mike Hull, for lending me your precious time, hands, and stories.
Brett Yasko, for essentially teaching me a year’s worth of book design in three weeks. Dylan Vitone, for making all my photography and lighting dreams come true. Together, for being the best capstone professors I could have asked for.
Wayne Chung, for graciously advising this project and for your expertise, support, and care.
Josiah Stadelmeier, for help with wiring and de-burring.
Adam Tripp, Todd Rodgers, and the rest of the design team at Forms + Surfaces, for the champions of education, innovation, and community that you are and your incredible generosity in making this project possible.
Classmates and dear friends Ricky Chen, Bryce Li, Teresa Lourie, Catherine Liu, and more.
Thank you for helping make my Senior Capstone everything I dreamed and more.